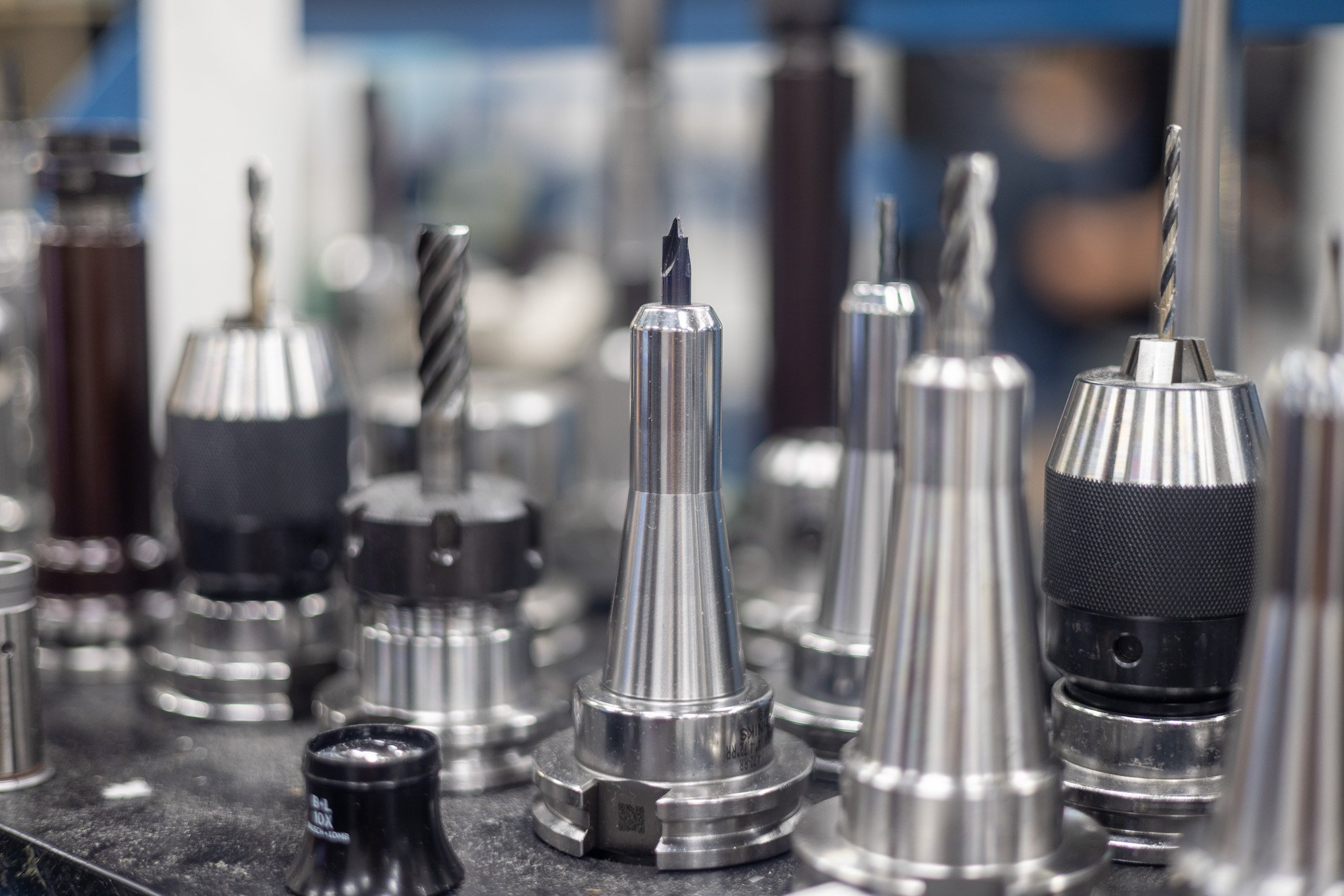
Moldmaking
JDM is dedicated to producing precision top quality molds for all types of products and industries.
-
Injection molding is a method to obtain molded products by injecting plastic materials molten by heat into a mold, and then cooling and solidifying them. The method is suitable for the mass production of products with complicated shapes and takes a large part in the area of plastic processing.
-
Liquid injection molding is the process used with liquid silicone rubber (LSR) to fix the material from an uncured state into a cured part.
-
Compression molding is a tried-and-true method of manufacturing simple rubber parts. The process is akin to waffle-making — a given amount of uncured rubber is placed into a mold cavity, which is then closed and heated. When the parts have cured, they are removed from the mold.
-
Rubber injection molding successfully alters the plastics process by heating the rubber and placing it under significantly more pressure per square inch of cavity surface in molding. Through various innovations, injection molding has become one of the most efficient ways to create molded rubber products in many cases.
-
Transfer molding is typically used for thermoset materials and is slightly different than traditional compression molding. It is a combination of injection and compression molding processes. In this process the polymer is preheated in a holding chamber called the pot.
-
The injection transfer molding process is a variation of the compression transfer molding process where the transfer unit in the top of the form will be filled with plastified rubber through the injection unit of the injection molding machine. The transfer of already plastified rubber compound allows a smoother filling of the mold.
JDM has the capabilities to polish or texture your mold or part to a variety of industry standards.
Turning
Complex turning projects are one of our specialties, with our selection of lathes we are able to produce simple and complex turned parts. Our lathes are able to accomplish more than just turning, with dual spindle and dual turrets, we are able to manufacture complex features within the machine.
-
Our dual spindle/single turret machine is capable of large production volumes. This lathe is equipped with ‘’live tooling’’. Live tooling allows us to produce small drill/milled features along the part. This machine is able to utilize both spindles simultaneously, reducing cycle time along with reducing part cost. With it’s bar feeder, this lathe can run around the clock.
-
Our dual spindle/dual turret machine is also capable of large production volumes. With it’s dual turrets, this machine is capable of producing parts in both spindles while drilling/milling. This is one of our most capable machines, the ability to run ‘’lights out’’ greatly reduces cost.
-
Referred to as our ‘’Swiss machine’’, we utilize our Citizen L20 to produce very large qty, intricate parts. This machine is able to run 24/7 also utilizing a bar feed system to keep material fed at all times. We are able to cut a wide variety of materials ranging from 6AL-4V Titanium, to Peek and other plastics.
-
Our remaining lathes typically produce component parts for prototyping, tool and die, and short run projects. These machines regularly work on parts that involve complex threading, as well as hard material (up to 58-60 HRC). Turning tight O.D./I.D. tolerances have become an alternative to some applications where grinding may have been used.
Milling
There are many ways to bring a project from idea to reality. We use our 3,4, and 5 axis mills to do just that. Depending on part size and geometry, we are able to program, setup, and run your parts with minimal setups. Reducing the number of setups = Less cost and lead time involved with your project. We are willing to take on any job large or small.
-
A few part examples that can be produced in a 3 axis mill include:
• Fixture plates
• Mold bases
• End of arm tooling -
Some of the capabilities produced in a 4 axis mill include:
• Helix or Helical designs
• Channels or grooves on round parts
• Angled features within or on the surface of a part. -
5 axis milling has allowed manufacturing the ability to produce complex parts that were previously thought to be impossible. Parts and features that can be produced using a 5 axis mill include:
• Turbine Blades
• Drafted helical surfaces
• 3D surfaces within a part
• Tighter tolerances between datum structures, (this is direct result of reduced setups)
Heat Treat
Using our heat treat oven, we are able to heat treat and stress relieve materials with quick turnaround. Below is a list of materials and hardness levels we are able to process.
-
Excellent resistance to wear from sliding contact with other metal or abrasive materials.
-
Widely used for making molds and dies.
-
Used for knife blades, shear blades, mold cores, and mold inserts.
-
Used for making knives, slitters, punches, tool holders, and woodworking cutting tools.
-
Used for bending and forming dies and shearing applications
-
Widely used in rolling contact bearings, mold cores, and mold inserts.
-
Stress-relieving is a technique to remove or reduce the internal stresses created in metal.
EDM
There are many instances where an undercut or sharp corner needs to be manufactured within a part. Turning and milling have their limitations. Although with our EDM department we are able to design, program, and burn features that would otherwise be impossible to cut.
-
Referred to as ‘’Sinker EDM’’, this process typically uses carbon or copper to electrically erode material. The piece of carbon or copper used is called the ‘’Electrode’’. The machinist will determine the best size and design of electrode for the application. Once the electrode is produced, it is then loaded in the EDM and charged with an electrical current to burn away unwanted material.
-
A wire EDM uses a small wire, typically .010’’ diameter, although there are smaller sizes depending on the application. The Wire EDM is used to produce thin features in very thick material. The wire is electrically charged and will erode or remove the material to produce a cut the width of the wire. You can think of a wire EDM almost like a ‘’Cookie Cutter’’.
Engineer
-
Our dedicated project managers collaborate with you and your team as a single point of contact, maintaining effective communications throughout each project. Our skilled project management team combines experience and technical expertise. Production planning and tracking keep your project on schedule.
-
In house design for various types of molds
• Plastic injection
• Compression
• Rubber injection
• LSR
• Transfer
• Injection Transfer -
Do you have a part with no prints or Cad model?
Bring us your part(s), and we will measure it, reconstruct it as a 3D model, and provide a print or Cad model back to you with your completed parts.
-
• SolidWorks®
• Mastercam®
• ESPRIT®